Row wire rod
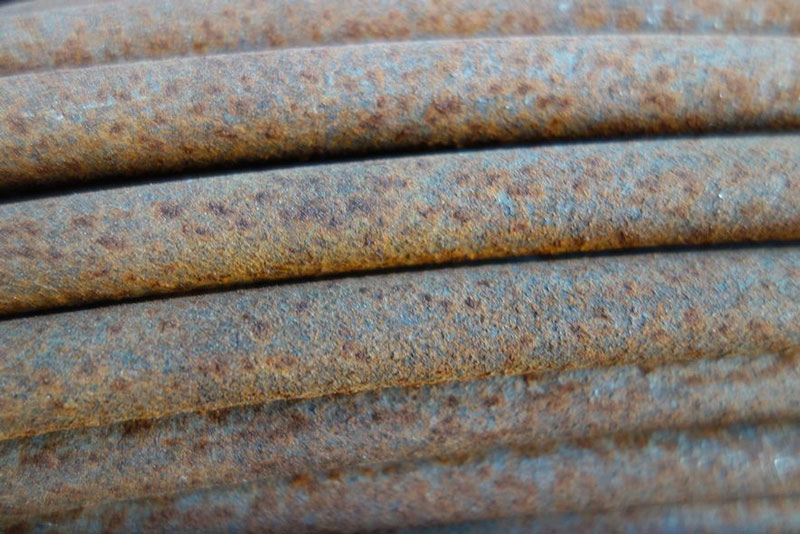
The wire rod is subsequently propelled by a horizontal wire rod pay-off system in a combined pull-in, bending and straightening machine (BDM-2S / EG). The scale layer is broken and the wire is straightened without cracks. The wire pull in is considerably facilitated by this system concept.
In the following double-head sanding descaler (SEZ-6-302S), the wire will be cleaned and surface pre-treated for the further coating process through two sanding belts with min. 100% cleanliness result.
The next wire preparation step is done by an electro-phosphating plant (Ephos®) Inline from STAKU.
Production range:
For Example:
Mechanical descaling with inline phosphating at the same drawing speeds as conventionally pickled wires without sacrificing quality.
Wire inlet ø8.0 – 15.0mm
Wire outlet drawing speed up to 10m/s
Wire inlet speed up to 1.5m/s
Download product data sheet (PDF)
Horizontal pay-off with coil pusher, model HAF/CVE
Pull-in – bending and straightening with model BDM/2S-EG
Mechanical descaling with double-head sandbelt descaler, model SEZ-6-302S